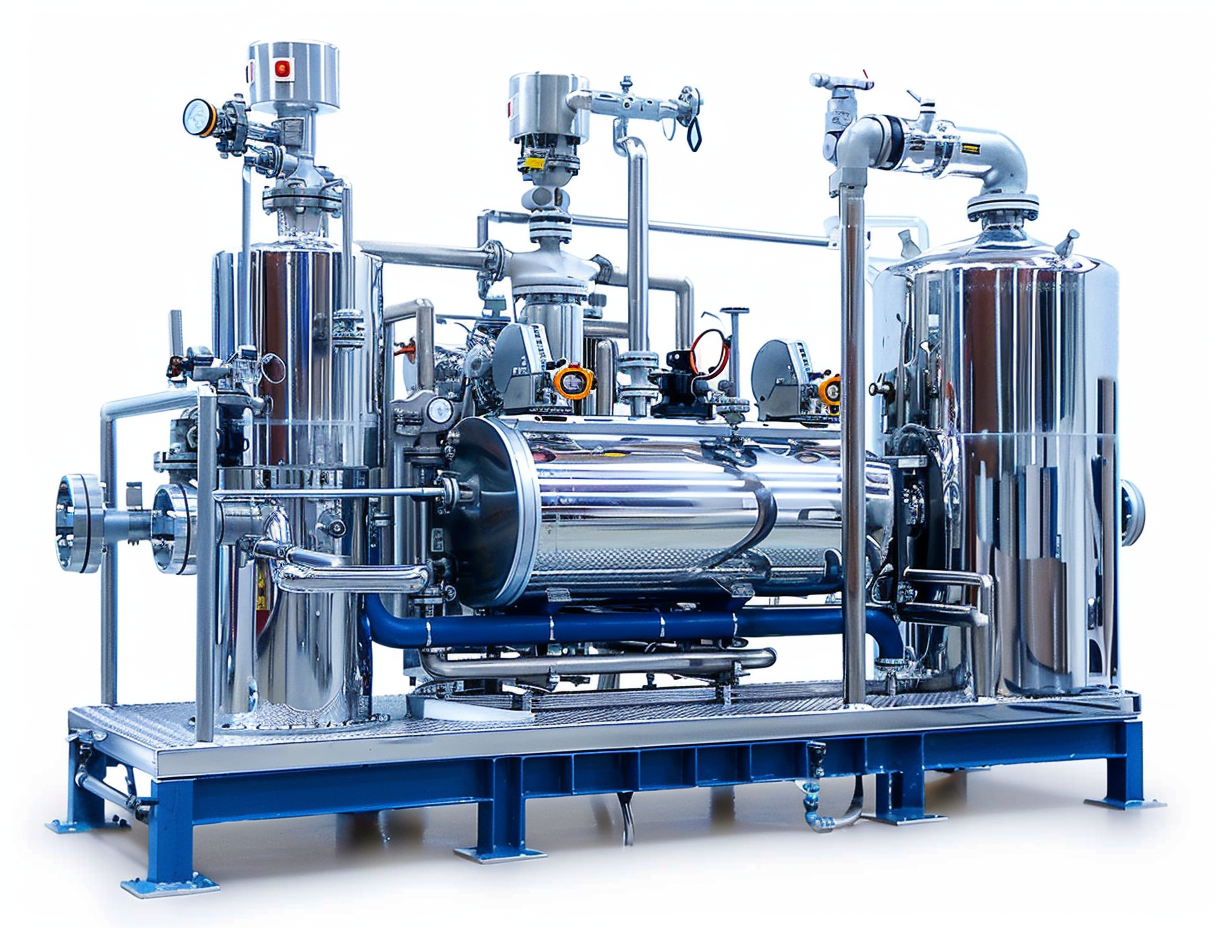
Understanding the Quadruple Effect Evaporator
An evaporator is a critical component in various industrial processes used for concentrating solutions by evaporating the solvent, typically water. The efficiency of this process can be significantly enhanced by using a multiple effect evaporator system. A quadruple effect evaporator includes four stages (or effects) to achieve high energy efficiency by reusing the vapor generated in one stage to heat the subsequent stages.
A quadruple effect evaporator is a type of multiple effect evaporator that includes four stages for maximizing energy efficiency. It utilizes the vapor from each stage to heat the following stage, thereby reducing the overall steam consumption and operational costs.
Working Principle of Quadruple Effect Evaporator
1. Feed Solution Introduction and Initial Conditions
The feed solution, which needs to be concentrated, is introduced into the first stage of the evaporator system. Each stage consists of an evaporator vessel, heat exchanger, and associated components.
2. Steam Supply to the First Stage
Steam is supplied to the first stage (effect) of the evaporator. The heat from this steam causes the solvent in the feed solution to evaporate. The evaporated solvent is called the vapor, and this vapor carries latent heat energy.
3. Heat Transfer to Subsequent Stages
The vapor generated in the first stage is not condensed immediately. Instead, it is used as the heating medium for the second stage. This process continues:
- Vapor from the first stage heats the second stage.
- Vapor from the second stage heats the third stage.
- Vapor from the third stage heats the fourth stage.
4. Sequential Evaporation
Each subsequent stage operates at a progressively lower pressure and temperature than the previous one. This pressure gradient allows the vapor from one stage to have sufficient thermal energy to evaporate the solvent in the next stage.
5. Final Stage and Condensation
In the fourth and final stage, the remaining vapor is condensed using cooling water or other methods. The solvent is collected, and the concentrated solution exits the evaporator system.
Components of Quadruple Effect Evaporators
1. Evaporator Vessels
Each stage has an evaporator vessel where the feed solution is heated, and evaporation occurs. These vessels are designed to handle the specific temperature and pressure conditions of each stage.
2. Heat Exchangers
Heat exchangers facilitate the transfer of thermal energy from the vapor of one stage to the solution in the next stage. They are crucial for maintaining efficient heat exchange and minimizing energy loss.
3. Vacuum System
A vacuum system is often employed to maintain the lower pressure in subsequent stages, ensuring that the evaporation process occurs at the required temperatures. This system helps optimize the temperature gradient across the stages.
4. Condenser
The condenser is where the final vapor is condensed back into the liquid solvent. Effective condensation is essential for maintaining the overall efficiency of the system.
5. Steam Trap and Separator
Steam traps and separators handle the separation of vapor from the liquid phase. They ensure that only vapor is used for heating subsequent stages, preventing any liquid carryover that could hinder the evaporation process.
Advantages of Quadruple Effect Evaporators
1. High Energy Efficiency
Quadruple effect evaporators achieve high energy efficiency by reusing vapor from each stage to heat the next stage, significantly reducing the amount of fresh steam required.
2. Lower Operational Costs
Due to decreased steam consumption, operational costs are lower. The reduced energy requirement translates to savings in fuel and utility expenses.
3. Environmentally Friendly
By improving energy efficiency and reducing steam consumption, quadruple effect evaporators have a lower environmental impact compared to single effect systems. They contribute to reduced greenhouse gas emissions and overall energy conservation.
4. Scalability and Flexibility
Quadruple effect evaporators can handle large volumes and are scalable for various industrial applications. They are flexible and can be adapted to different operating conditions and feed solutions.
5. Improved Process Control
The multi-stage design allows for better process control, enabling precise adjustments to optimize performance and efficiency. This control is critical for industries requiring stringent specifications and consistency.
Applications of Quadruple Effect Evaporators
1. Food and Beverage Industry
- Concentration of Juices and Syrups: Efficiently concentrating fruit juices and syrups while preserving flavors and nutritional properties.
- Dairy Processing: Used for concentrating milk and whey.
2. Chemical Industry
- Concentration of Chemicals: Ideal for concentrating various chemical solutions and recovering solvents.
3. Pharmaceutical Industry
- Active Ingredient Concentration: Concentrating active pharmaceutical ingredients (APIs) efficiently and consistently.
4. Wastewater Treatment
- Effluent Treatment: Reducing the volume of industrial wastewater by removing water content, making the effluent easier to handle and dispose of.
5. Desalination
- Salt Water Concentration: Used in desalination plants to concentrate saltwater and recover freshwater.
Factors Influencing the Performance of Quadruple Effect Evaporators
1. Feed Solution Properties
The physical and chemical properties of the feed solution, including viscosity, boiling point elevation, and thermal sensitivity, affect the efficiency and effectiveness of the evaporation process.
2. Heat Exchanger Design
The design, material, and heat transfer efficiency of the heat exchangers play a crucial role in maintaining optimal thermal conditions and ensuring efficient heat exchange between stages.
3. Operating Conditions
Maintaining the correct pressure and temperature gradients across the stages is essential for optimal performance. Any deviations can impact the overall efficiency and output.
4. Maintenance and Fouling
Regular maintenance and monitoring for fouling (buildup on heat exchange surfaces) are necessary to ensure continuous and efficient operation. Fouling can significantly reduce heat transfer efficiency and increase energy consumption.
Conclusion
A quadruple effect evaporator is an advanced and efficient multiple effect evaporator system that utilizes four stages to maximize energy efficiency by reusing vapor for heating subsequent stages. This design significantly reduces steam consumption and operational costs, making it suitable for a wide range of industrial applications, including the food and beverage industry, chemical processing, pharmaceuticals, wastewater treatment, and desalination.
Understanding the working principle, components, advantages, and applications of quadruple effect evaporators can help in selecting the right system for specific needs, ensuring optimal performance, energy conservation, and cost-effectiveness.
FAQ
- What is a quadruple effect evaporator?
A quadruple effect evaporator is a multiple effect evaporator system consisting of four stages that utilize the vapor from one stage to heat the next, maximizing energy efficiency. - How does a quadruple effect evaporator work?
It works by introducing feed solution into the first stage, heating it to evaporate the solvent, then using the vapor from each stage to heat the subsequent stage, progressively reducing steam consumption. - What are the advantages of using a quadruple effect evaporator?
Advantages include high energy efficiency, lower operational costs, reduced environmental impact, scalability, flexibility, and improved process control. - In what industries are quadruple effect evaporators commonly used?
They are used in the food and beverage industry, chemical industry, pharmaceutical industry, wastewater treatment, and desalination. - What factors influence the performance of quadruple effect evaporators?
Factors include feed solution properties, heat exchanger design, operating conditions, and regular maintenance to prevent fouling.