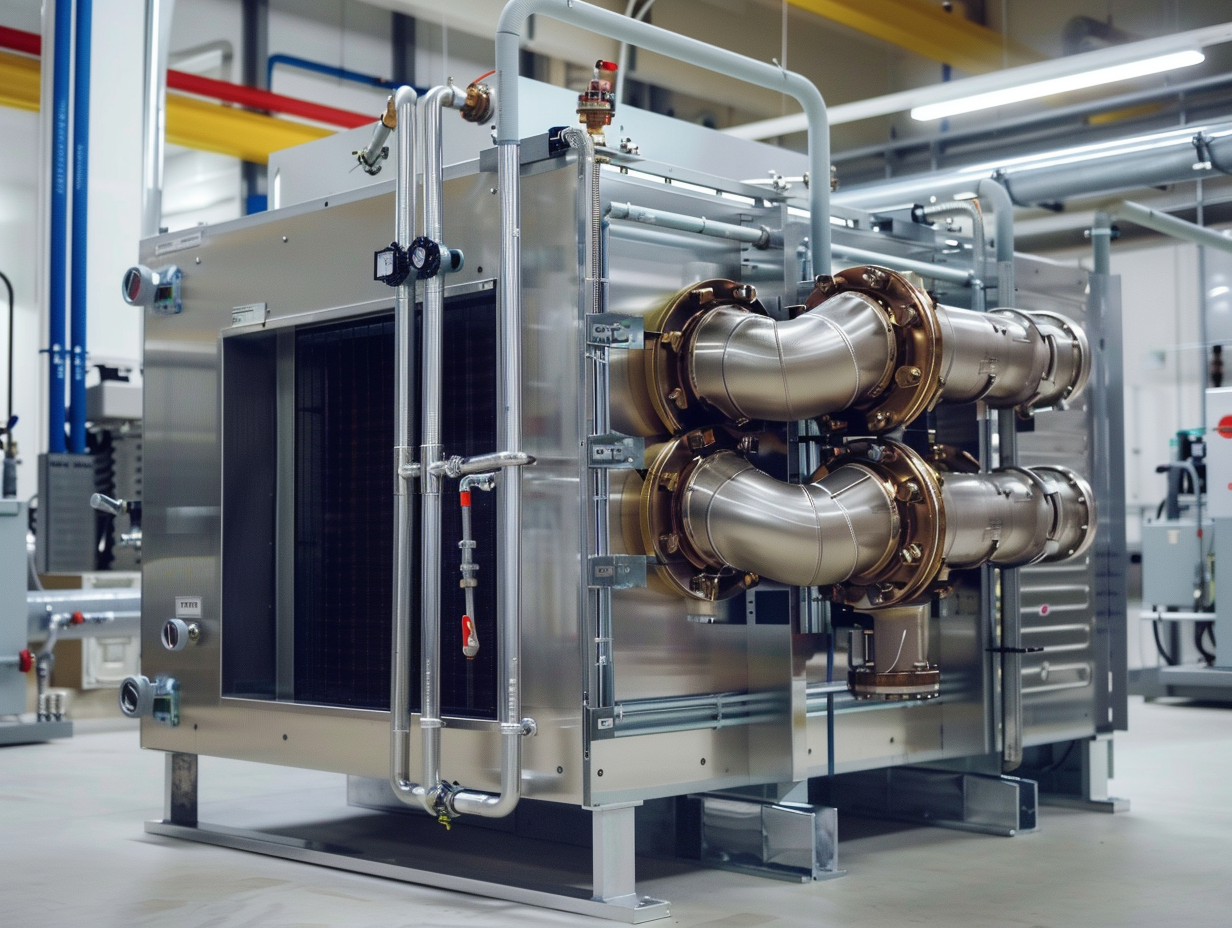
Understanding the Difference Between TVR and MVR Evaporators
Both Thermal Vapor Recompression (TVR) and Mechanical Vapor Recompression (MVR) evaporators are advanced technologies used to enhance the efficiency of the evaporation process by recycling vapor. Despite their similar end goals, they achieve vapor recompression through different mechanisms. Understanding the differences between these two types of evaporators can help in selecting the most suitable system for specific industrial applications.
The primary difference between TVR and MVR evaporators lies in the method used for vapor recompression. TVR evaporators use steam ejectors to compress vapor, while MVR evaporators use mechanical compressors.
Thermal Vapor Recompression (TVR) Evaporator
Overview
In a TVR evaporator, a steam ejector is used to compress and recycle the vapor generated during the evaporation process. This system is often integrated into multiple effect evaporators to enhance energy efficiency.
Working Principle
- Evaporation Process: The feed solution is introduced into the evaporator, where heat causes the solvent (typically water) to evaporate.
- Vapor Generation: The generated vapor is directed to the steam ejector.
- Steam Ejector: The steam ejector uses high-pressure steam to entrain the vapor. The mixture of the high-pressure steam and vapor is then compressed to a higher pressure.
- Vapor Reuse: The recompressed vapor is reused as a heating medium in the evaporator, reducing the need for fresh steam.
Key Components
- Evaporator Vessel: Where the feed solution is heated and vaporized.
- Steam Ejector: Utilizes high-pressure steam to entrain and compress the vapor.
- Condenser: Condenses the final vapor for solvent collection.
- Heat Exchanger: Facilitates efficient heat transfer between the vapor and the feed solution.
Advantages
- Increased Energy Efficiency: By recycling vapor, TVR systems reduce the demand for fresh steam, leading to energy savings.
- Lower Operational Costs: Reduced steam consumption translates to lower operational costs.
- Simple and Robust Design: Fewer moving parts compared to mechanical systems, resulting in lower maintenance requirements.
Disadvantages
- Dependency on Steam Supply: The system relies on a constant supply of high-pressure steam, which can be costly and may limit applications in areas with steam constraints.
- Limited Efficiency Gains: While more efficient than single effect systems, TVR systems are generally less efficient than MVR systems.
Applications
- Food and Beverage Industry: Concentrating juices and syrups.
- Chemical Industry: Concentrating chemical solutions.
- Pharmaceutical Industry: Concentrating active ingredients.
Mechanical Vapor Recompression (MVR) Evaporator
Overview
In an MVR evaporator, a mechanical compressor is used to compress and recycle the vapor generated during the evaporation process. This system is known for its high energy efficiency and is increasingly popular in various industrial applications.
Working Principle
- Evaporation Process: The feed solution is introduced into the evaporator, where heat causes the solvent to evaporate.
- Vapor Generation: The generated vapor is directed to the mechanical compressor.
- Mechanical Compressor: The compressor mechanically compresses the vapor to a higher pressure and temperature.
- Vapor Reuse: The recompressed vapor is reused as a heating medium in the evaporator, significantly reducing the need for external heat sources.
Key Components
- Evaporator Vessel: Where the feed solution is heated and vaporized.
- Mechanical Compressor: Compresses the vapor mechanically without requiring high-pressure steam.
- Condenser: Condenses the final vapor for solvent collection.
- Heat Exchanger: Facilitates efficient heat transfer between the vapor and the feed solution.
Advantages
- High Energy Efficiency: MVR systems offer superior energy efficiency by reusing vapor and minimizing the need for external heat sources.
- Reduced Operational Costs: The high efficiency leads to significant reductions in energy consumption and operational costs.
- Versatile Applications: Not dependent on high-pressure steam, making MVR systems suitable for a wide range of applications.
Disadvantages
- Higher Initial Cost: The mechanical compressors and related equipment result in higher upfront costs.
- Complexity and Maintenance: More complex systems with moving parts require regular maintenance and monitoring for optimal performance.
Applications
- Water Treatment: Wastewater evaporation and desalination.
- Food and Beverage Industry: Concentrating dairy products, juices, and other liquid foods.
- Chemical Industry: Concentrating chemical solutions and recovering solvents.
- Pharmaceutical Industry: Concentration of active pharmaceutical ingredients.
Comparison of TVR and MVR Evaporators
Energy Efficiency
- TVR: Utilizes steam ejectors to recycle vapor, providing improved efficiency over single effect systems but generally less efficient than MVR systems.
- MVR: Uses mechanical compressors to recycle vapor, offering the highest energy efficiency among vapor recompression systems.
Operational Costs
- TVR: Lower operational costs compared to single effect systems due to reduced steam consumption.
- MVR: Significantly lower operational costs due to superior energy efficiency and minimal reliance on external heat sources.
Initial Investment
- TVR: Generally lower initial cost due to simpler design and fewer components.
- MVR: Higher initial cost due to the complexity and cost of mechanical compressors and related equipment.
Maintenance Requirements
- TVR: Lower maintenance requirements due to fewer moving parts.
- MVR: Higher maintenance requirements due to the complexity and mechanical components that need regular servicing.
Application Flexibility
- TVR: Depends on the availability of high-pressure steam, which may limit its application in certain settings.
- MVR: More versatile and can be used in a wider range of applications due to its independence from high-pressure steam.
Conclusion
Thermal Vapor Recompression (TVR) and Mechanical Vapor Recompression (MVR) evaporators both enhance the efficiency of evaporation processes by recycling vapor, but they operate using different mechanisms. TVR evaporators use steam ejectors and rely on high-pressure steam, making them simpler and often less costly initially but somewhat limited in efficiency. MVR evaporators use mechanical compressors, offering superior energy efficiency and versatility at a higher initial cost and greater complexity.
Choosing between TVR and MVR evaporators depends on specific application requirements, including energy efficiency goals, operational cost considerations, available resources (e.g., steam supply), and budget constraints.
FAQ
- What is the main difference between TVR and MVR evaporators?
The main difference is the method of vapor recompression: TVR uses steam ejectors, while MVR uses mechanical compressors. - Which system is more energy-efficient, TVR or MVR?
MVR evaporators are generally more energy-efficient due to their use of mechanical compressors to recycle vapor. - What are the maintenance requirements for TVR and MVR evaporators?
TVR systems have lower maintenance requirements due to fewer moving parts, while MVR systems require more maintenance due to the complexity and mechanical components. - What types of applications are suitable for TVR evaporators?
Suitable applications include food and beverage processing, chemical concentration, and pharmaceutical ingredient concentration, where steam supply is readily available. - Can MVR evaporators be used for wastewater treatment?
Yes, MVR evaporators are commonly used for wastewater evaporation and desalination due to their high energy efficiency and versatility.