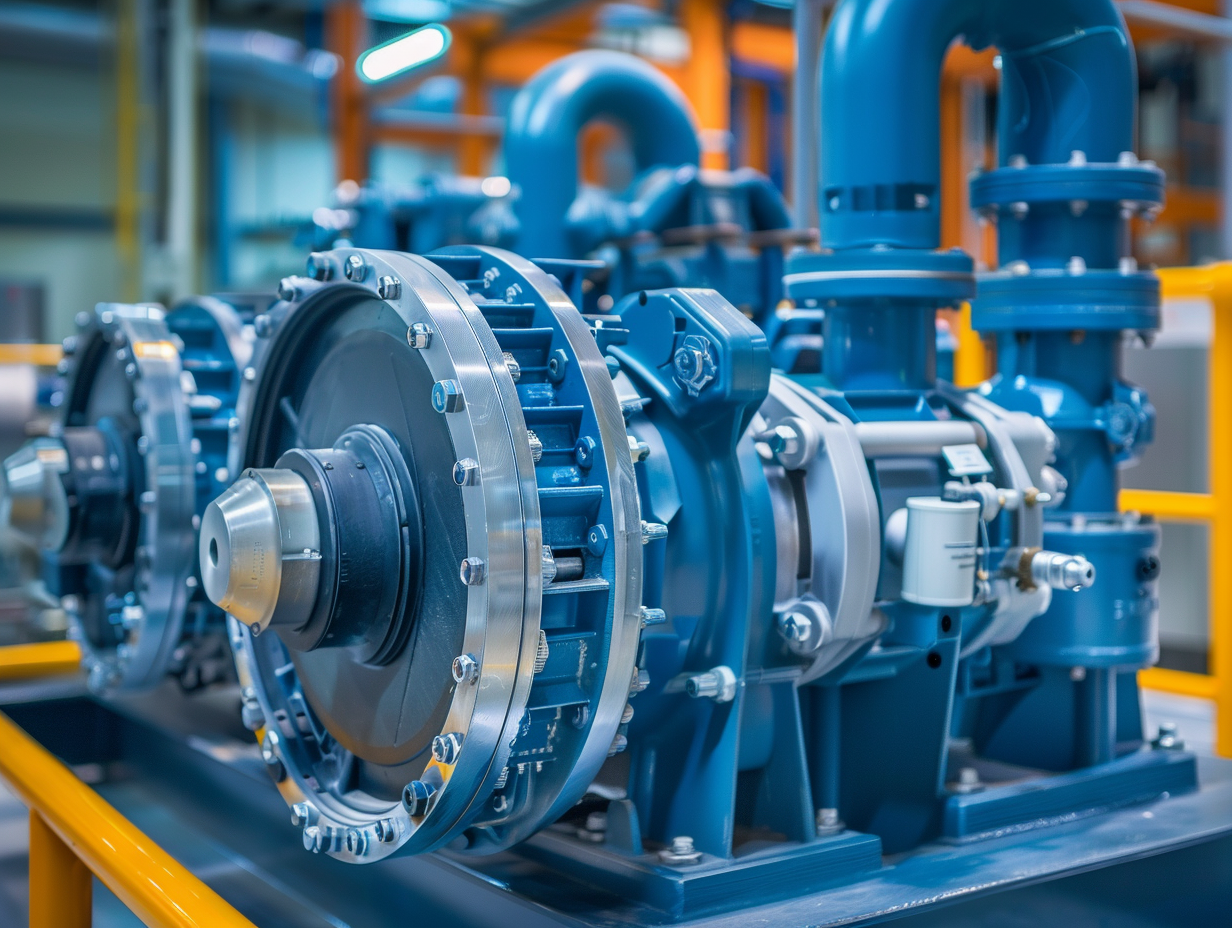
Understanding the Difference Between a Compressor and a Centrifugal Pump
Both compressors and centrifugal pumps are vital components in various industrial and engineering applications, but they serve distinct purposes and operate based on different principles. Understanding the differences between these two devices is crucial for selecting the appropriate equipment for a specific application.
The primary difference between a compressor and a centrifugal pump lies in the type of fluid they handle and their operational principles. Compressors are designed to pressurize and move gases, while centrifugal pumps are used to transport liquids through the conversion of rotational kinetic energy into hydrodynamic energy.
Fundamental Differences
1. Type of Fluid Handled
Compressors
- Fluid: Compressors are used to compress and move gases, including air, nitrogen, helium, and other gases.
- Properties: Gases are compressible fluids that can change volume significantly under pressure.
Centrifugal Pumps
- Fluid: Centrifugal pumps are designed to move liquids, including water, oils, chemicals, and slurries.
- Properties: Liquids are incompressible fluids with relatively constant volume under pressure.
2. Operating Principle
Compressors
- Compression: Compressors increase the pressure of a gas by reducing its volume. This process involves compressing gas, which may also result in an increase in temperature.
- Working Cycle: Typically involves stages of compression, cooling, and sometimes storage of the compressed gas.
Centrifugal Pumps
- Centrifugal Force: Centrifugal pumps utilize a rotating impeller to impart kinetic energy to the liquid. The centrifugal force generated pushes the liquid outward to the pump casing, converting kinetic energy to hydrodynamic energy.
- Flow: The liquid enters the pump through the suction inlet, passes through the rotating impeller, and exits through the discharge outlet at a higher pressure and flow rate.
Design and Components
Compressors
Types of Compressors
- Reciprocating Compressors: Use pistons driven by a crankshaft to deliver gas at high pressure.
- Rotary Compressors: Utilize rotating elements (e.g., screws, vanes) to compress gas.
- Centrifugal Compressors: Use a rotating impeller to add velocity to the gas, converting it to higher pressure.
Key Components
- Cylinder and Piston (Reciprocating Compressors): Components that compress gas within a cylinder.
- Rotors (Rotary Compressors): Moving parts that compress gas through rotational motion.
- Impeller (Centrifugal Compressors): Rotating component that increases gas velocity.
- Intercoolers and Aftercoolers: Used to cool the gas between and after compression stages to remove excess heat.
Centrifugal Pumps
Types of Centrifugal Pumps
- Single-Stage Pumps: Feature one impeller for general liquid transport applications.
- Multi-Stage Pumps: Contain multiple impellers for higher pressure and flow rate applications.
- Submersible Pumps: Designed to operate while submerged in the fluid being pumped.
Key Components
- Impeller: The rotating part that imparts kinetic energy to the liquid.
- Casing: The outer shell that directs the flow of liquid through the pump.
- Suction and Discharge Ports: Inlets and outlets for fluid entry and exit.
- Seal and Bearings: Prevent fluid leakage and support the rotating shaft.
Applications
Compressors
- Industrial Processes: Used in chemical plants, refineries, and manufacturing to provide pressurized air or gas.
- HVAC Systems: Compressors in air conditioning and refrigeration systems compress refrigerant gases.
- Pneumatic Systems: Provide the necessary pressurized air for pneumatic tools and equipment.
- Gas Transmission: Compress natural gas for transportation through pipelines.
Centrifugal Pumps
- Water Supply: Used in municipal water supply systems to transport water from sources to storage and distribution points.
- Irrigation: Provide the necessary pressure and flow rate for agricultural irrigation systems.
- Chemical Processing: Transfer chemicals, solvents, and other industrial liquids.
- Wastewater Treatment: Pump wastewater and sludge in treatment plants.
Efficiency and Maintenance
Compressors
- Efficiency: The efficiency of a compressor is influenced by factors such as pressure ratio, type of compressor, and method of cooling.
- Maintenance: Requires regular inspection of components like pistons, cylinders, rotors, and coolers to ensure optimal performance and longevity. Lubrication and sealing are critical maintenance tasks.
Centrifugal Pumps
- Efficiency: Efficiency depends on factors like the impeller design, the flow rate, and the total head. Pumps are generally more efficient at their best efficiency point (BEP).
- Maintenance: Routine maintenance includes checking the impeller for wear, inspecting seals and bearings for leaks and wear, and ensuring proper lubrication.
Operational Considerations
Compressors
- Pressure Control: Compressors need to manage varying pressure demands, often equipped with pressure regulators and safety valves.
- Thermal Management: Managing the heat generated during compression is essential, necessitating cooling methods (air-cooled or water-cooled).
Centrifugal Pumps
- Flow Control: Centrifugal pumps manage flow rates rather than pressure. Valves and variable speed drives are commonly used for flow regulation.
- Cavitation: A phenomenon where vapor bubbles form and collapse in the pump, potentially causing damage. Preventive measures include maintaining adequate suction head and avoiding excessive flow rates.
Conclusion
The primary difference between compressors and centrifugal pumps lies in the type of fluid they handle and their operating principles. Compressors are designed to pressurize and move gases using various compression techniques, while centrifugal pumps transport liquids through the conversion of rotational kinetic energy into hydrodynamic energy.
Choosing between a compressor and a centrifugal pump depends on the specific requirements of the application, including the type of fluid, desired pressure or flow rate, and operational considerations. Understanding these differences and their respective components, applications, efficiency, maintenance needs, and operational factors is essential for selecting the right equipment.
FAQ
- What is the primary difference between a compressor and a centrifugal pump?
The primary difference is the type of fluid they handle: compressors are designed for gases, while centrifugal pumps are designed for liquids. - Can a centrifugal pump be used to compress gases?
No, centrifugal pumps are not suitable for compressing gases as they are designed to move incompressible fluids like liquids. - What are some common applications of compressors?
Common applications include industrial processes, HVAC systems, pneumatic systems, and gas transmission. - How does a centrifugal pump operate?
A centrifugal pump operates by using a rotating impeller to impart kinetic energy to the liquid, which is then converted into hydrodynamic energy to transport the liquid. - What maintenance tasks are essential for centrifugal pumps?
Essential maintenance tasks include checking the impeller for wear, inspecting seals and bearings, and ensuring proper lubrication to maintain optimal performance.